New energy inverter
The heat sink of the new energy inverter is very important, as it plays a crucial role in ensuring the high temperature and stable operation of the chip, while also extending its service life and improving the efficiency of power generation
Our Businesses
Get a Quotation
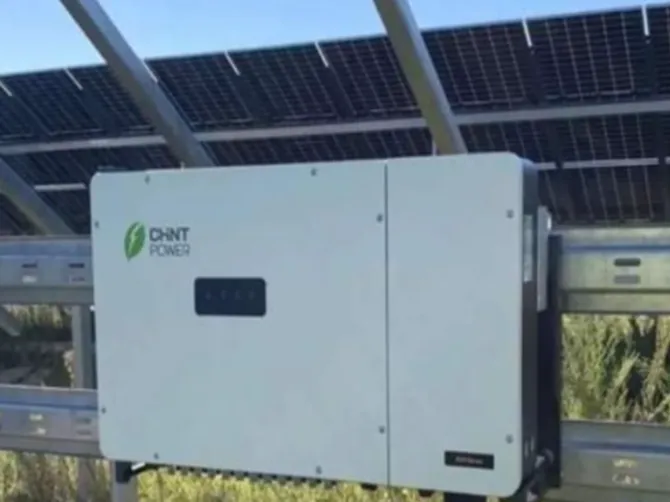

New energy inverter thermal managent:
The Necessity of Heat Dissipation
During the operation of a new energy photovoltaic inverter, power devices inevitably generate a large amount of heat. Take the common centralized inverter as an example, the IGBT modules inside will release a considerable amount of heat energy when operating at full load. If this heat cannot be dissipated in a timely manner, it will cause a sharp increase in the internal temperature of the inverter. Studies have shown that for every 10°C increase in the internal temperature of the inverter, the lifespan of electronic components will be shortened by approximately 50%, and it will also lead to a decrease in the conversion efficiency, thus seriously affecting the overall performance and stability of the photovoltaic power generation system. Therefore, efficient heat dissipation is of vital importance for ensuring the reliable operation of the photovoltaic inverter, extending its service life, and improving the power generation efficiency.
The Function of the Heat Sink
As the core component of the heat dissipation system of the photovoltaic inverter, Walmate thermal heat sink mainly achieves efficient heat dissipation through two ways: increasing the heat dissipation area and promoting heat transfer. Take the aluminum alloy Skived fin heat sink, as an example, its unique fin structure greatly increases the contact area with the air, enabling the heat to be transferred to the surrounding air more quickly. At the same time, the heat sink is usually used in conjunction with thermal conductive silicone grease, which can fill the tiny gaps between the power devices and the heat sink, effectively reducing the thermal resistance and further enhancing the heat transfer effect, ensuring that the heat generated by the inverter can be dissipated rapidly and efficiently.
Types of Heat Sinks
Natural Cooling Heat Sinks:
Natural cooling heat sinks do not rely on any external power and dissipate heat only through natural convection and radiation. Generally produced using Die-casting technology.It has a very simple structure, low cost, and no noise during operation, making it suitable for string inverters with relatively small power (generally less than 20kW) and relatively low heat dissipation requirements. In some small distributed photovoltaic power generation projects, the natural cooling heat sink can meet the heat dissipation requirements of the inverter, and because it does not require additional power consumption, it has a high cost-performance ratio.
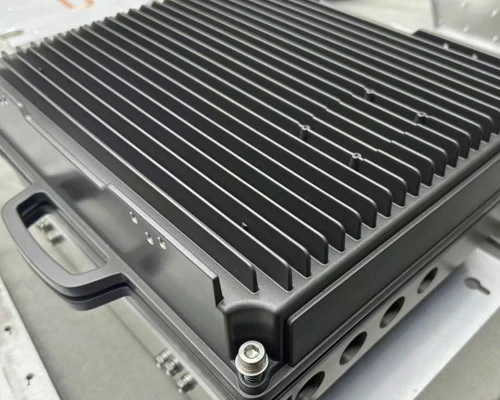
Forced Air Cooling Heat Sinks:
Forced air cooling heat sinks force the air to flow through devices such as fans to take away the heat. Its heat dissipation efficiency is significantly higher than that of natural cooling heat sinks, and it is suitable for inverters with relatively large power (generally greater than 25kW). In centralized photovoltaic inverters with a power range of 100kW – 1MW, forced air cooling is a common heat dissipation method. However, forced air cooling also has some disadvantages. For example, the fan will generate noise during operation, and it requires a certain amount of electrical energy consumption. At the same time, dust is likely to enter the device, which may affect the normal operation of the device.
At present, due to the cost pressure on the client side, many solutions are for small volume and high-power inverter applications, which greatly increases the demand for heat dissipation performance of the heat sinks. Therefore, Walmate Thermal’s design scheme is to increase the heat pipe at the bottom of Skived fin heat sink under the same volume and size of radiator conditions, achieving rapid heat conduction and greatly improving the heat conduction and heat dissipation performance of the heat pipe heat sink per unit time
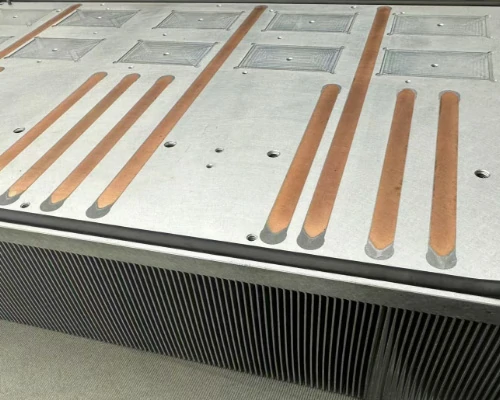
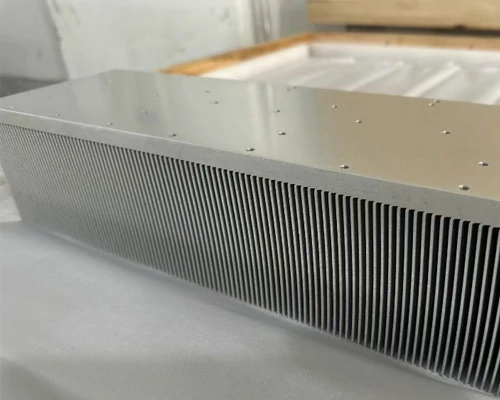
Key Points for Selecting Heat Sinks
-Power Matching:
Select an appropriate heat sink according to the power of the inverter. Generally speaking, the greater the power, the more heat is generated, and the stronger the required heat dissipation capacity. For small-power inverters, natural cooling heat sinks can be selected; while for high-power inverters, forced air cooling or liquid cooling heat sinks are required to ensure the heat dissipation effect.
-Environmental Adaptability:
Consider the usage environment of the inverter, such as temperature, humidity, dust, and other factors. In high-temperature, high-humidity, or dusty environments, it is necessary to select heat sinks with good protection performance to prevent the heat sinks from being corroded or blocked, which will affect the heat dissipation effect. The surface treatment of the heat sink is also very important, usually by powder coating or anodizing.For example, in photovoltaic power stations in desert areas, due to the large amount of sand and dust, a forced air cooling heat sink with a high protection level should be selected and equipped with an effective dust-proof device,At the same time, attention should also be paid to the spacing between fins in the heat sink design to prevent dust from clogging the air vents.
Under the premise of meeting the heat dissipation requirements, comprehensively consider the cost of the heat sink. The costs of different types of heat sinks vary greatly. The natural cooling heat sink has the lowest cost, and the liquid cooling heat sink has the highest cost. It is necessary to select the heat sink with the highest cost-performance ratio according to the project budget and actual needs.
Application of New Technologies
Heat Pipe Heat Dissipation Technology:
The heat pipe is an extremely innovative heat transfer element, standing out with its extraordinary thermal conductivity. Its working principle is based on the evaporation and condensation process of the internal liquid within a fully sealed vacuum tube. Driven by fluid dynamics principles such as capillary action, the heat pipe can achieve rapid heat transfer, thus enabling efficient heat dissipation and easily handling the heat dissipation challenges in various high-heat generation scenarios.
Heat pipe heat sinks possess remarkable advantages. They not only have ultra-high thermal conductivity and excellent isothermal characteristics, ensuring uniform heat distribution and avoiding local overheating, but also allow the heat transfer areas at both the hot and cold ends to be flexibly adjusted according to actual needs. In addition, it has the ability to transfer heat over long distances, breaking through spatial limitations for heat transfer, and it can also precisely control the temperature. Whether in electronic devices, industrial machinery, or the aerospace field, it can become an ideal heat dissipation solution thanks to these features.
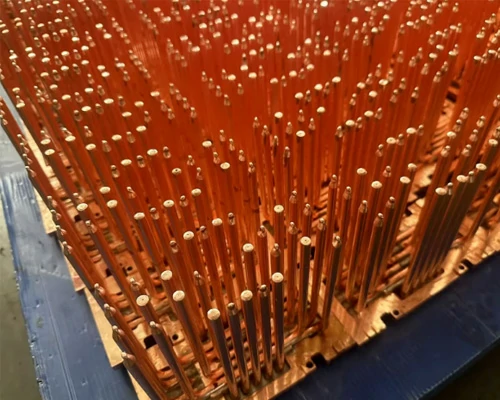
Heat Dissipation Simulation Technology:
Walmate Thermal utilizes Ansys simulation software to provide customers with highly realistic simulations of the thermal conditions within inverter systems. During the design phase, this advanced software enables us to accurately predict the operating temperature values of each component, offering valuable insights into the system’s thermal behavior.
By meticulously analyzing the simulation results, we can promptly identify and rectify any unreasonable structural layouts in the inverter. This proactive approach significantly shortens the design and R&D cycle, effectively reducing costs associated with trial-and-error processes. Moreover, it enhances the product’s first-pass success rate, ensuring that our customers receive high-quality, reliable inverter solutions that meet their thermal management requirements right from the start.
