Liquid cold plates
It is a device component that solves the heat problem of high-power chips. They utilize circulating coolant to efficiently remove and transfer heat from high-power components. The optimized flow channel design ensures uniform cooling, improves system reliability, and extends equipment lifespan.
What is a liquid cooling plate?
The liquid cold plate is an innovative thermal management tool that breaks through the limitations of traditional heat dissipation methods. It surpasses the inherent bottleneck of the thermal conductivity of solid materials. By constructing a precise internal fluid network, it transforms heat transfer from a single solid-state conduction mode into a composite heat dissipation mode combining solid and liquid coupling.The core of its design lies in the exquisite application of fluid dynamics. The winding layout of the flow channels, the precise aperture size, and the design of the turbulence structures are all aimed at maximizing the contact area between the coolant and the wall surface. Meanwhile, it ensures that the fluid achieves efficient heat exchange under low-resistance conditions.
This heat dissipation solution is particularly suitable for modern devices with exponentially increasing power density. When the heat generated by core components such as chips and batteries is like a concentrated heat source bursting out, the liquid cold plate acts like an intelligent temperature manager. Through the circulation of the coolant, it quickly captures and disperses the heat, controlling the temperature fluctuation within a very small range.What’s more remarkable is that the liquid cold plate can be customized according to different application scenarios. From miniature electronic components to megawatt-level energy storage systems, by adjusting the flow channel topology, the type of coolant, and the circulation pressure, it can meet the differentiated heat dissipation requirements, thus building a reliable thermal protection barrier for the stable operation of high-power equipment.
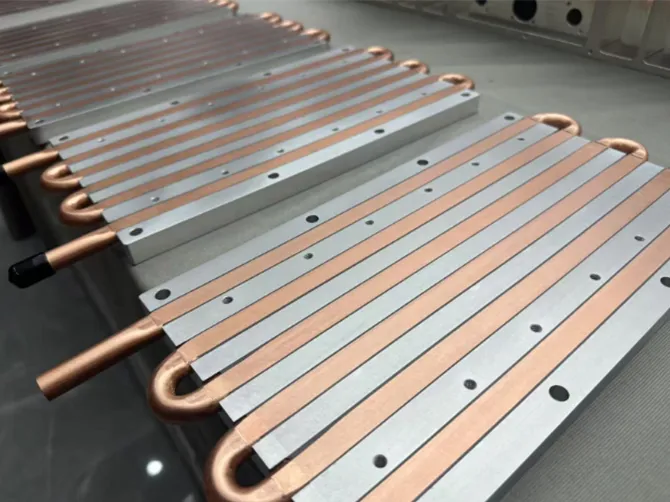
Round tube liquid cooling plate
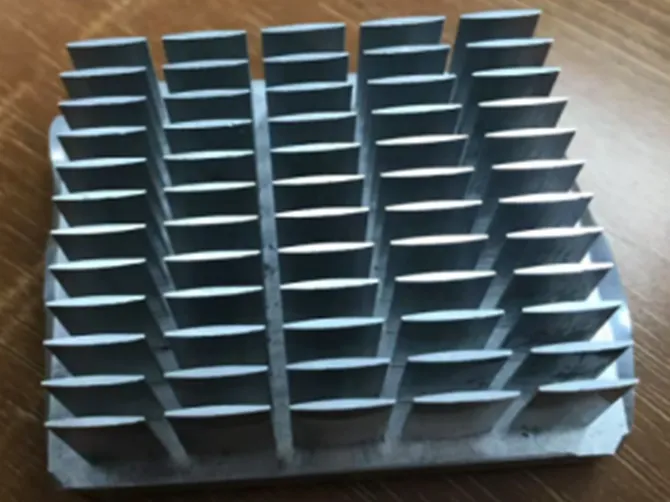
Round tube liquid cold plate
How to produce a suitable liquid cold plate for customers?
We need to accurately determine the size and shape of the liquid cooling plate, as well as the layout of internal microchannels and flow channels, based on actual application requirements such as chip power size, specific heat dissipation indicators, etc. Using computer-aided design software for 3D modeling and do the thermal solutions, then continuously optimizing through computational fluid dynamics simulation, to ensure that the coolant can flow uniformly and avoid eddies, achieving the best heat dissipation effect.
It is crucial to select the appropriate process when manufacturing liquid cold plates. For chips with a power output of less than 1 kilowatt, due to their relatively low heat generation, a simple flow channel design can meet the heat dissipation requirements. Such liquid cold plates can be directly formed with simple flow channels through CNC machining. Alternatively, copper tubes or stainless steel tubes can be bent and then embedded at the bottom of the liquid cold plate. These two processes are simple, reliable, and can effectively control costs.
For high-power IGBT devices, the power often exceeds 3000 watts, generating a large amount of heat. The common simple flow channels and processing methods are difficult to ensure the heat dissipation effect. For these devices, it is necessary to carry out refined processing on the flow channels at the contact part between the liquid cold plate and the chips, Usually, the Skived fin process is adopted to machine micro-channel structures in local areas. Then, through friction stir welding or brazing technology, all components are precisely welded to form the final product, so as to improve the heat dissipation efficiency and ensure that the IGBT operates at a stable temperature.
Provide thermal design analysis soltuions for our clients
Our thermal engineer provides professional liquid cold plate design services, leveraging the powerful Ansys Icepack software for all preliminary design work. Once clients share essential parameters, including the chip’s power and dimensions, the desired length, width, and height of the liquid cold plate, coolant flow rate, temperature, and the specific usage environment, our engineers immediately get to work. We start by creating detailed 3D models in the software, conducting in – depth thermal analyses to understand heat transfer dynamics thoroughly. Based on the analysis results, we optimize the micro – channel structure for maximum heat dissipation efficiency. Considering both the performance requirements and our practical manufacturing costs, we carefully select the most suitable production process, ensuring that the final design is not only highly effective but also cost – efficient for our clients.
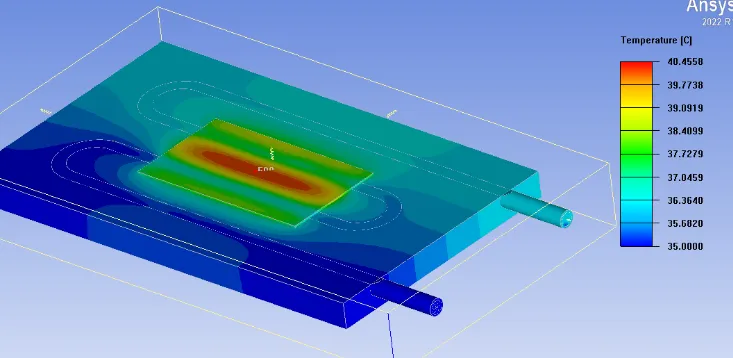
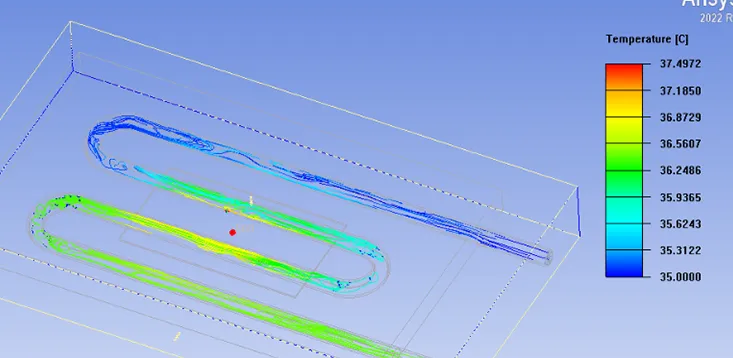
Ensure the reliability of the liquid cold plate.
Once production is completed, we will conduct a series of comprehensive leak tests, which are tailored to the customer’s product. Normally, we double the actual working pressure of the water pump in the customer’s liquid cooling circulation system. For example, if the customer’s water pump pressure is 0.7 megapascals, we will conduct a pressure holding test for 30 to 45 minutes at a pressure of approximately 1.5 megapascals. To ensure the accuracy of the testing, we have adopted various testing methods. Air detection helps to quickly detect larger leakage points, helium detection can provide high-precision results, and even the smallest defects can be accurately located. Liquid circulation testing simulates the actual usage environment, ensuring that the flow channel of the liquid cooling plate will not leak in various situations.