Extrusion heat sink
It refers to a heat - dissipation device manufactured via extrusion technology, with fin - shaped structures for enhanced heat transfer and component protection.
What is a extruded heat sink?
Profile heat sink or extrusion heat sink is a common heat dissipation device, mainly made of metal profiles such as 6061 or 6063 aluminum alloy . Through concave convex shaped molds, the aluminum alloy is heated to a high temperature of around 450 degrees to soften. The temperature of copper alloy is 750-800 degrees.Then, based on the designed fin thickness and spacing, a heat sink device with a base plate and fin is formed by high-pressure extrusion. Utilize the principles of heat conduction and convection to achieve heat dissipation. The heat from the heat source is conducted to the substrate, and then distributed to the fins by the substrate. The heat is dissipated through natural or forced convection of the air.
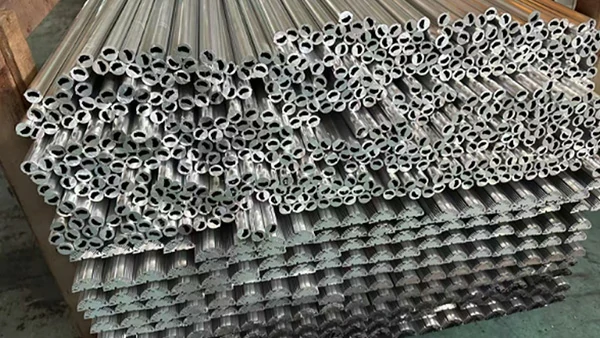
Characteristics of extruded heat sinks
High Heat Dissipation Efficiency
Using extrusion molding technology, copper alloy or aluminum alloy metal materials can be quickly extruded into specific shapes in molds, with high production efficiency and suitable for large-scale production, which can effectively reduce costs.
Strong customizability
By designing different molds, various shapes, sizes, and structures of profile heat sinks can be manufactured to meet personalized requirements such as fin thickness, height, and spacing for different devices, installation spaces, and heat dissipation requirements.
Surface quality
The extruded profile has a smooth surface, reducing the workload of subsequent surface treatment. At the same time, good surface quality helps to improve the heat dissipation efficiency of the heat sink, especially for TEC module heat sink. The smooth surface is not easy to condense water droplets.
Excellent mechanical properties
During the extrusion process, the internal structure of the metal material is optimized, resulting in profile heat sinks with good mechanical properties such as strength and stiffness, which can withstand certain external forces and vibrations, ensuring reliability during use.
Pay attention to the relationship between fin and spacing during design the extruded heat sink.
In the design of extrusion heat sinks, the ratio between the fin gap and height is closely related to the machining process. A too large ratio may complicate the metal fluid flow in the mold during extrusion, leading to insufficient fin filling and deformation. A too small ratio can greatly increase the machining difficulty and even cause severe mold wear and a shortened lifespan due to the small mold gap.
Warmate Thermal are equipped with extrusion machines ranging from 600 to 8000 tons, enabling us to precisely control the manufacturing process. In practice, a fin gap-to-height ratio of 1:24 is found ideal. When the fin height is 24 mm, the gap is set at 1 mm. This ratio not only makes the most of our extrusion machines but also ensures good fin quality, stays within the machining precision range, and balances machining feasibility and heat dissipation efficiency.
When designing the fin height, one should avoid blindly pursuing excessively large dimensions, because overly tall fins will significantly impede the effective transfer of heat. Tapered fins are a preferable choice, with a root thickness set at 2 millimeters and a tip thickness of 1 millimeter. This shape not only facilitates the rapid conduction of heat but also provides ample space for heat dissipation. Meanwhile, it reduces the resistance during the fan’s operation, remarkably enhancing the overall heat dissipation efficiency and ensuring the stable operation of the heat dissipation system.

Attention to the application of profile heat sinks
Profile heat sink, with the advantage of the extrusion molding process, have notable merits like low production costs and high production efficiency, and are widely applied in the heat dissipation field. However, their heat dissipation performance is restricted by the design of the fin thickness and spacing. If the fins are too thick or the spacing is too wide, the heat dissipation area per unit size will decrease correspondingly. Conversely, if one tries to blindly reduce the size to increase the area, issues such as a sharp increase in processing difficulty and a decline in structural strength will arise. When compared with radiators fabricated by complex processes such as brazing, profile radiators struggle to create a super-large heat dissipation surface area within a limited space. Thus, they are unable to meet the rigorous heat dissipation demands of high-power density chips and are usually more suitable for the heat dissipation of low-power chips. Still, for customers who prioritize cost control and have relatively modest heat dissipation requirements, profile radiators remain an excellent and cost-effective option.
What can we do for our customers?
Warmate Thermal offers comprehensive solutions for customers in the field of extrusion heat sinks. Our minimum order quantity is 300 kilograms, which enables us to meet the needs of different customers, whether for small-scale projects or large-scale productions. We are equipped with extrusion machines ranging from 600 to 8000 tons, allowing us to customize heat sinks according to specific requirements, precisely adjusting the thickness, height, and spacing of the fins to optimize the heat dissipation efficiency.
We use imported steel to make the molds, ensuring that the molds have excellent quality and durability. This not only guarantees the precision of our products but also enhances their structural integrity. Our experienced team provides professional design consultations, helping customers balance costs and performance. Throughout the production process, we also ensure strict quality control to guarantee that the products have excellent structural strength and surface finishing effects. Whether it is a low-power application pursuing cost-effectiveness or a project with specific size and installation limitations, we can provide reliable and high-quality extrusion heat sinks, improving the performance and service life of our customers’ products.
When customers are engaged in product design and are unable to determine the subsequent demand for the time being, we also offer a flexible mold fee refund policy. Generally speaking, when customers purchase more than 20 tons of materials, we will refund the mold fee based on the amount of the mold fee. For example, if the mold fee is less than 10,000 yuan, we will refund the mold fee after the customer purchases 10 tons of materials; if the mold fee is around 100,000 yuan, we will refund it after the customer purchases 20 tons of materials. This policy aims to reduce the customers’ upfront investment costs and help them plan their production more flexibly.