Extrued profile liquid cold plates
Extruded liquid cooling plates are made via profile extrusion. The flow channels are formed in one step, offering an efficient, cost-effective solution for heat dissipation.
Get a Quotation
What is a extrued liquid cooling plate?
liquid cooling plate in profile process is a kind of product that utilizes a profile mold to directly extrude and form the flow channels. It doesn't require any additional subsequent processing to shape the structure of the flow channels. This production method omits the complex procedures in the flow channel processing of traditional liquid cooling plates. It achieves one-step molding through the mold, which greatly improves production efficiency and reduces production costs. It is widely applied in fields such as electric vehicles and battery energy storage that are sensitive to costs and production efficiency.
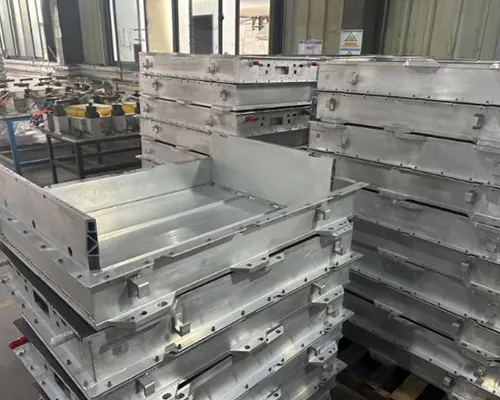

How to make a extrued liquid cooling plate?
In the production and manufacturing of profile liquid cooling plates, the first and foremost step is to design and plan the flow channels of the liquid cooling plates based on the actual application conditions. Take a liquid cooling plate with a width of 400 millimeters and a thickness of 10 millimeters as an example. Generally, the wall thickness is designed to be between 1.5 and 2 millimeters. In this way, the effective height of the middle flow channel is approximately 6 millimeters. At the same time, according to the results of thermal analysis, the number of flow channels is rationally planned, usually designed to be between 8 and 12 channels. By precisely designing the corresponding mold and using the profile extrusion process, the material is processed into a hollow plate, whose structure is similar to that of a harmonica. Thus, the first step of the production of the liquid cooling plate is completed.
Then, based on the number of formed flow channels, we scientifically plan the flow direction of the coolant. Taking a liquid cooling plate with 8 flow channels as an example, we set the first and second channels as the coolant inlets, and successively design the third and fourth channels, the sixth and seventh channels, as well as the eighth channel as the outlets. Through this series connection layout, the original 8 independent flow channels are integrated into 4 orderly coolant circulation paths. Subsequently, we use the argon arc welding process to weld and seal the end plates. With the high-efficiency fusion performance and reliable sealing property of argon arc welding, we ensure that the coolant can flow uniformly throughout the entire flow channel system, giving full play to the heat dissipation function of the liquid cooling plate and improving the overall heat dissipation efficiency and stability.
After completing the planning of the flow channels and the welding of the end plates, we enter the final stage of the liquid cooling plate manufacturing. First, we weld two water cooling connectors to the first and second channels respectively, which serve as the inlets for the coolant. At the same time, the seventh and eighth channels are clearly designated as the outlets. In this way, once the two water cooling connectors are welded, the entire set of flow channels forms a series-connected channel system. Customers only need to connect these two ports of the water cooling connectors to effectively cool the battery modules or other heating elements.
To ensure the product quality and safety in use, all the manufactured liquid cooling plates must undergo a pressure holding test to detect their sealing performance and check for any leakage. If a leakage problem is found during the test, we will immediately carry out secondary welding on the corresponding parts until the product passes the pressure holding test. Finally, we will deliver liquid cooling plate products with high reliability and stable performance.
The largest width size of cold plate we can produce
– Aluminum alloy integrated structure design, maximum width of 1200mm
– Adapted for large-scale/high-load scenarios, material costs are reduced by 5-15%, and structural weight is reduced by 10-20%.
– Increase in lifecycle reliability by 200% ,Meet high-voltage cascaded coolant requirements

Our standard liquid cooling plate specifications and sizes
In order to meet the needs of customers and reduce their development costs and time in the future, we have developed a series of standard products for customers to choose .
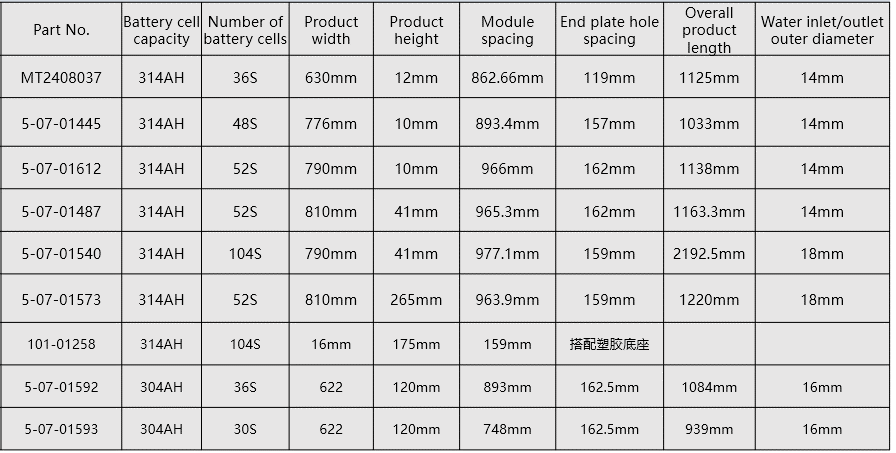

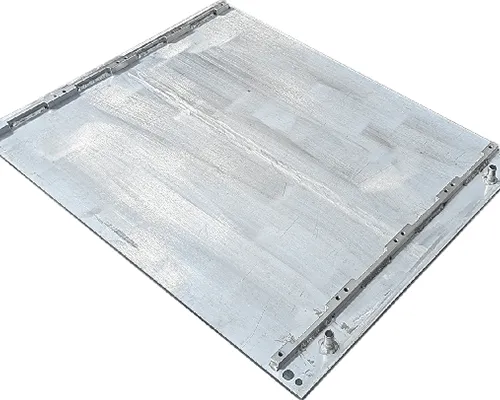
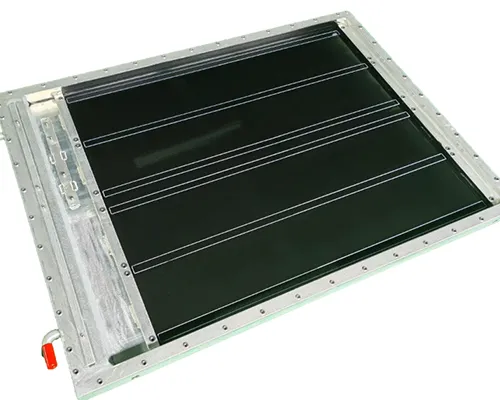
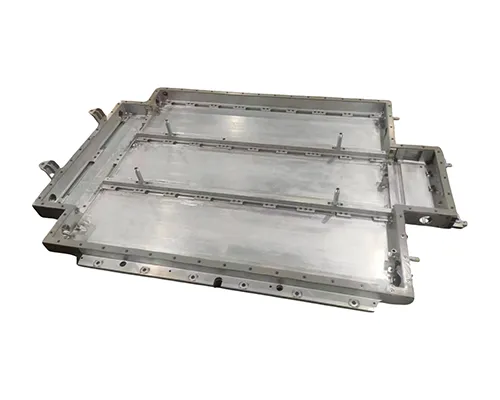
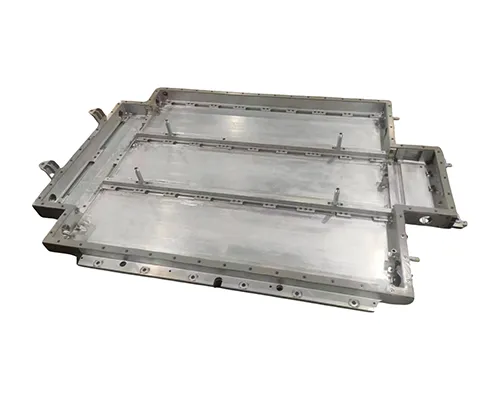
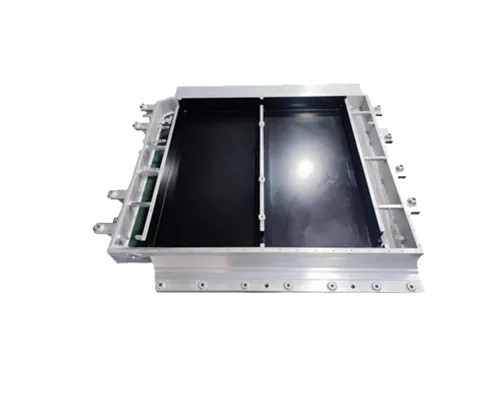
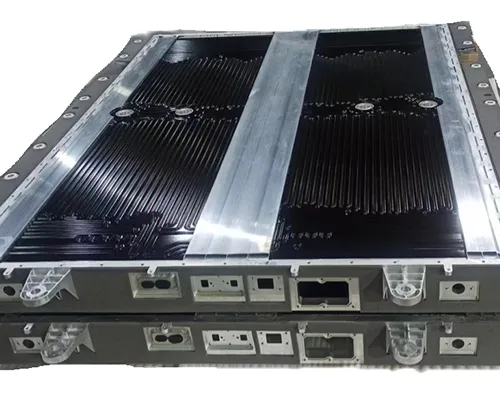
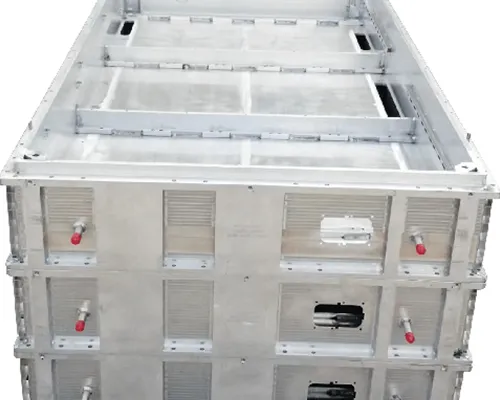