Die-casting heat sink
Using die-casting technology, aluminum alloy and other metal materials are injected into molds under high pressure to form heat dissipation components with complex structures.
What is a die-casting heat sink?
Die-cast heat sinks are important carriers in the industrial and civil heat dissipation fields. Relying on high-pressure die-casting technology, molten metal is injected into the mold cavity at high speed and pressure to form the product. Its core advantage lies in the high flexibility of structural design. By optimizing the fin density, thickness, and arrangement, it can achieve the best balance between the heat dissipation area and space utilization. It is especially suitable for scenarios with strict requirements for heat dissipation efficiency, such as electronic devices and thermal management systems of new energy vehicle batteries. Thanks to the application of lightweight and highly thermally conductive materials like aluminum alloy, while ensuring efficient heat dissipation, it effectively reduces the overall weight, meeting the lightweight requirements of modern equipment. In addition, the integrated die-casting molding process gives it excellent mechanical stability, enabling it to withstand vibrations and impacts under complex working conditions.
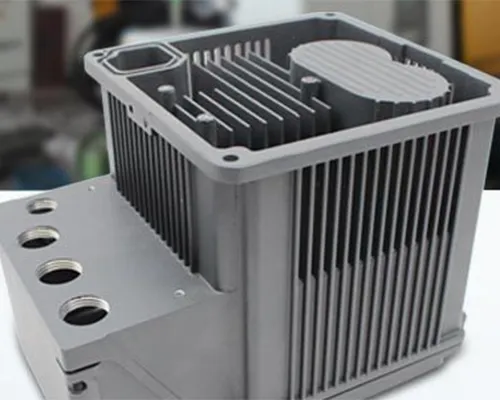
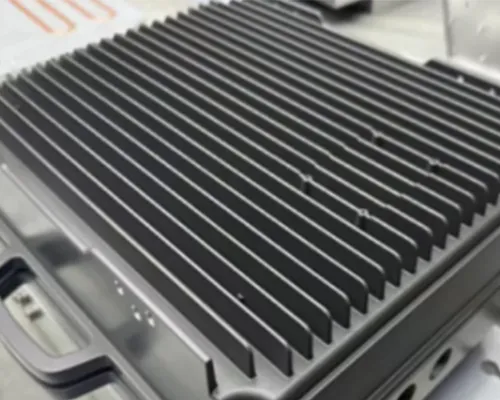
Characteristics of die-casting heat sinks
Die-casting heat sinks are generally used for heat sinks with large quantities and simple structures, and they have a relatively low power density, such as for chips with powers of 5 watts, 10 watts, or 50 watts. They are mainly used for exterior parts, like LED heat dissipation. Relying on their simple structure, they not only complete the structure of the lamps but also add the function of heat sinks, increasing the surface area and achieving the feature of meeting both structural and heat dissipation requirements.
The materials used in die-cast heat sinks each possess distinct advantages. Aluminum alloy, with a thermal conductivity of 180 – 230W/(m·K), dominates due to its lightweight nature and robust corrosion resistance, making it a go-to choice. Magnesium alloy, despite higher costs and susceptibility to corrosion, excels in high-end applications thanks to its ultra-light density of 1.8g/cm³ and thermal conductivity of 150W/(m·K). Zinc alloy, renowned for its superior castability, overcomes its 110W/(m·K) thermal conductivity limitation through innovative structural designs, fitting perfectly for consumer electronics.
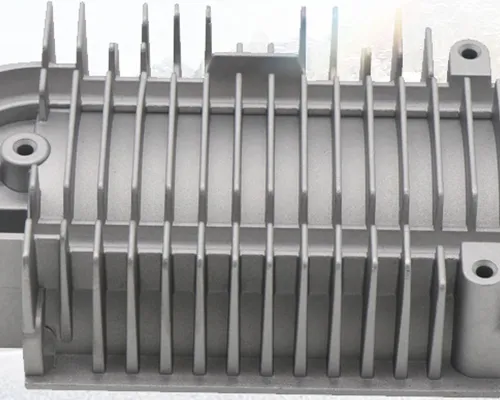
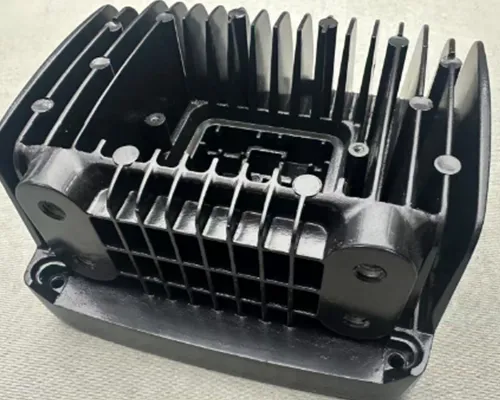
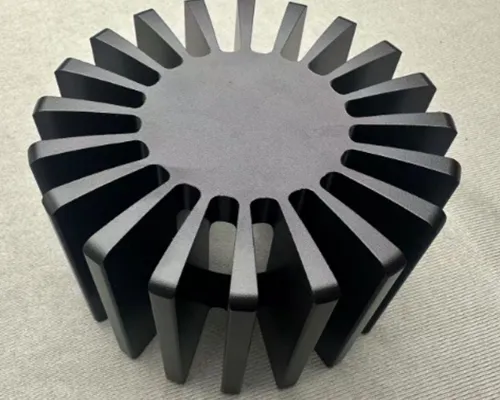
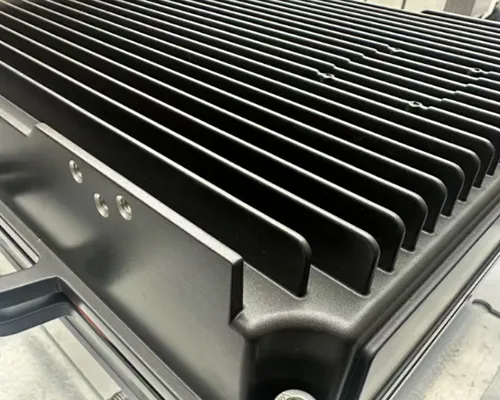