Deep drilling Liquid cold plates
It is a device component that solves the heat problem of high-power chips. They utilize circulating coolant to efficiently remove and transfer heat from high-power components. The optimized flow channel design ensures uniform cooling, improves system reliability, and extends equipment lifespan.
Get a Quotation
What is a deep hole drilling liquid cooling plate?
Deep hole drilling liquid cooling plate is an aluminum plate manufactured through mechanical processing. Specifically, a drill bit is used to machine holes of a certain depth in the aluminum plate. Subsequently, threaded plugs are used to block the corresponding inlet and outlet ports, thus forming a closed flow channel. Such an aluminum plate with a specific flow channel is the deep hole drilling liqid cooling plate.This kind of liquid cooling plate is simple to process and low in cost. It is also a commonly used liquid cooling device for heat dissipation in electronic devices.
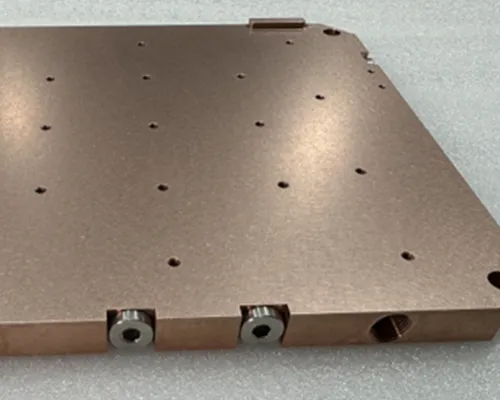
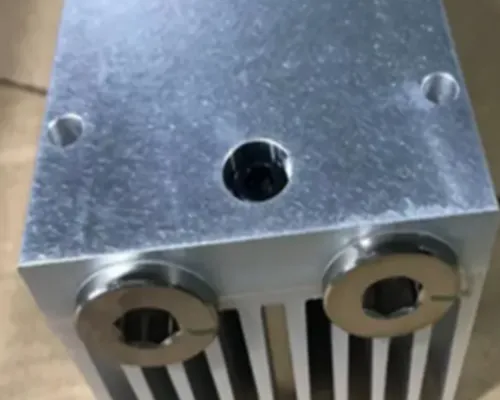
Characteristics of deep hole drilling liquid cooled plate
This kind of liquid cooling plate has remarkable advantages. Its flow channel design is simple, and the production efficiency is high. The specific processing procedure is as follows: usually, a drill bit with a diameter of 6 mm or 9 mm is used to drill on the aluminum plate. First, drill horizontally to a depth of 200 to 250 millimeters, and then drill about 100 millimeters from the side. After drilling four deep holes in the X-axis direction, drill through the first and second deep holes in the Y-axis direction to open up the first and second flow channels. Similarly, open up the third and fourth deep holes in the Y-axis direction. Finally, use the drill bit to connect the second and third deep holes in the X-axis direction to form a closed flow channel.
Based on the above processing method, this kind of liquid cooling plate demonstrates outstanding practical value and limitations. Due to its uncomplicated processing process, the cost can be effectively controlled, and it can flexibly meet the heat dissipation requirements of electronic devices of different sizes. However, this simple process is only applicable to the heat dissipation requirements of low-power devices. For situations with a relatively high power density, other methods need to be adopted. In fact, this process is a technical means that was used in the early days when friction stir welding and brazing had not yet emerged.