Brazing liquid cold plate
it is a liquid cooled plate production process that utilizes the micro diffusion of solder atoms and base materials in a vacuum environment to construct an integrated flow channel structure with zero leakage and high thermal conductivity
Get a Quotation
What is a vacuum brazed liquid cooling plate?
The manufacturing of liquid cooling plates through the brazing process is a production technique where two structures are welded together using brazing materials within a vacuum environment or under the protection of an inert gas atmosphere. During this process, the brazing materials, which have a melting point lower than that of the base materials, are heated to the point of melting. They then infiltrate and fill the gaps between the components to be joined. Through atomic diffusion and bonding, a strong connection is formed, ensuring that the liquid cooling plate has excellent sealing properties and thermal conductivity, meeting the heat dissipation requirements.
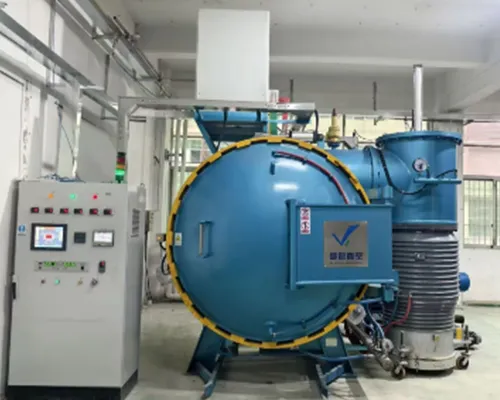
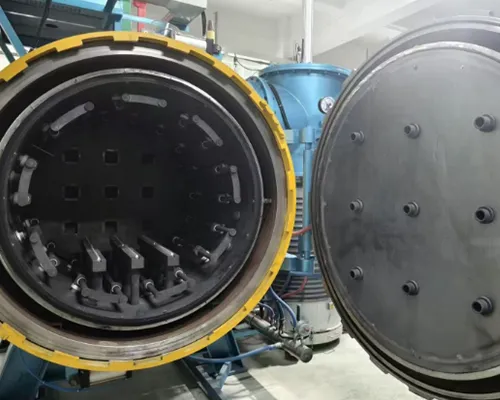
Characteristics of brazing liquid cooled plate
High welding quality
During the vacuum brazing process, oxidation can be avoided, ensuring that the filler metal can fully wet the surface of the vacuum brazed liquid-cooled plate. This will form high-strength and highly airtight welded joints, effectively improving the reliability and heat dissipation performance of the vacuum brazed liquid-cooled plate.
Minimal workpiece deformation
Due to the slow and uniform heating and cooling processes, the thermal stress can be greatly reduced, enabling the vacuum brazed liquid-cooled plate to maintain good dimensional accuracy. Even for complex structural components, the vacuum brazed liquid-cooled plate is not prone to deformation.
Clean and pollution-free
The entire welding process is carried out in a vacuum environment, without the interference of pollutants and without the generation of harmful gases. There is no need for complex post-welding cleaning work, thus ensuring the cleanliness of the vacuum brazed liquid-cooled plate
Wide application range
The vacuum brazing process is suitable for the welding of vacuum brazed liquid-cooled plates made of various metals and alloys, and can achieve the connection of different materials. In the field of data centers, the vacuum brazed liquid-cooled plates of AI servers often adopt this process for manufacturing to meet the heat dissipation requirements of high-power equipment.
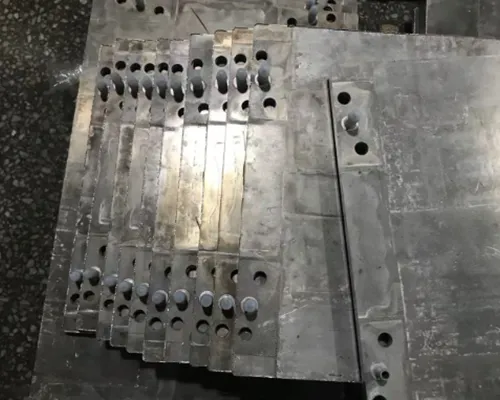
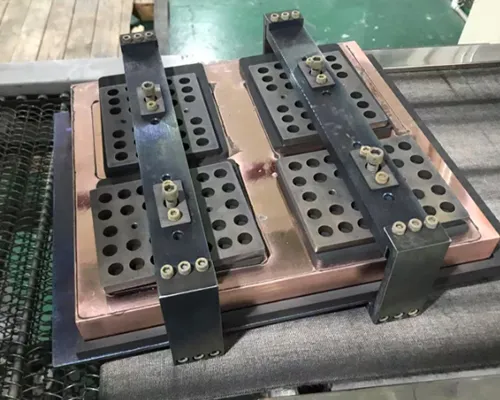
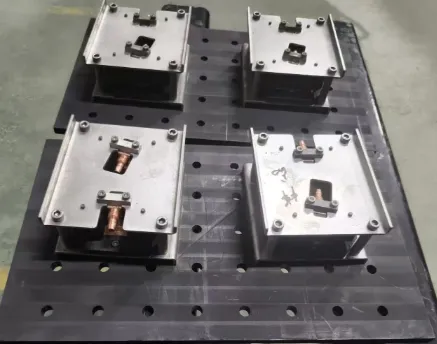
Brazing process liquid cooled plate for Intel Eagle Stream
The Material and Advantages:
Intel, in collaboration with Boyd and Envision, has launched a multi platform liquid cooled aluminum cold plate system that uses aluminum as the cold plate material and is produced through vacuum brazing technology. It has the characteristics of lightweight structure, flexible process, and significant economic advantages. Its performance is comparable to copper cold plates on the same platform, and it has obvious advantages in low thermal resistance, small temperature difference, and low flow resistance.
Design Features:
In the full liquid cold plate server project jointly developed by Intel and Inspur Information, the brazing process was also used to produce the CPU cold plate module. It is based on the design requirements of the Intel Xeon Eagle Stream platform expandable processor cold plate, and is optimized by considering factors such as heat dissipation, structural performance, yield, price, and compatibility of different material cold plate designs. It mainly consists of CPU cold plate aluminum brackets, CPU cold plates, and cold plate joints.
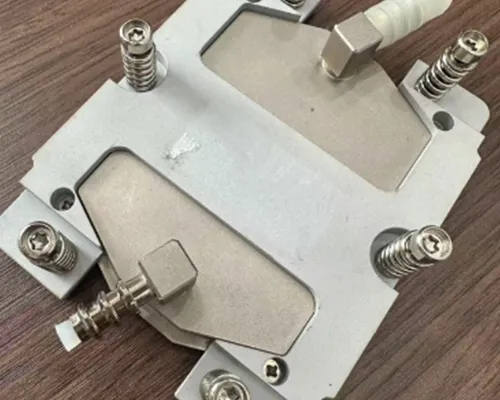
Brazing process liquid cooled plate for AMD SP5
AMD SP5 liquid cooling heads are designed to effectively dissipate heat for high-performance servers with AMD SP5-socketed CPUs.Some SP5 liquid cooling heads are made of a copper base and copper fins, which are connected through a precise pure copper brazing process. This brazing process ensures excellent heat transfer and structural stability. They usually measure about 118mm×92.4mm×19.1mm, with a weight of around 430g.
The benefits are significant. Copper has high thermal conductivity, enabling it to quickly absorb heat from the CPU. The brazed joints minimize thermal resistance between components, ensuring efficient heat transfer to the coolant. Such a design allows the liquid cooling head to handle a CPU TDP of up to 400W, maintaining the CPU at a stable operating temperature even under heavy loads, thus enhancing the overall performance and reliability of the server system.
Brazing process liquid cooled plate for Nvidia H100
As a high-performance computing card, the Nvidia H100’s liquid cooled plate and water-cooled head are crucial for maintaining stable performance. The liquid cooled plate of H100 is usually made of pure copper material and skived fin as microchannels, and is manufactured through vacuum brazing process. The brazing process carried out in a vacuum environment can effectively avoid material oxidation, ensure that the brazing material is fully fused and in contact with pure copper and copper fin, and form a strong and efficient connection structure. This process not only ensures the overall strength of the liquid cooled plate, but also greatly improves its thermal conductivity, which can quickly and evenly transfer the large amount of heat generated during the operation of H100, ensuring the stable operation of .
The brazed cooled plate also utilizes vacuum brazing technology to precisely bond components made of materials with excellent thermal conductivity, such as pure copper. This process minimizes the thermal resistance between the various parts of the water cooling head. With advanced cooling technology, the liquid cooling plate designed by Walmate Thermal has a heat dissipation capacity of 50W/℃ at a flow rate of 1LPM. The heat dissipation capacity, including the thermal interface material (TIM) and packaging, is 25W/℃, and the pressure drop is only 3psi. This allows the water cooling head to efficiently remove the heat generated by H100, even under long-term high load working conditions, helping H100 maintain excellent performance.
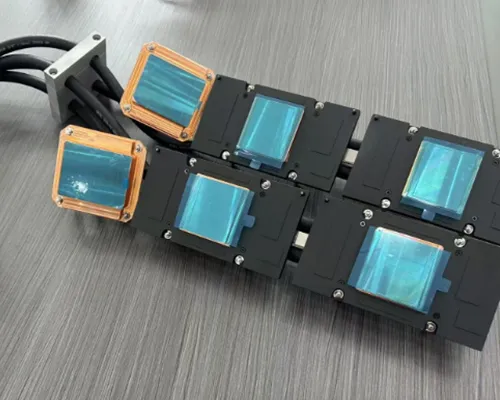
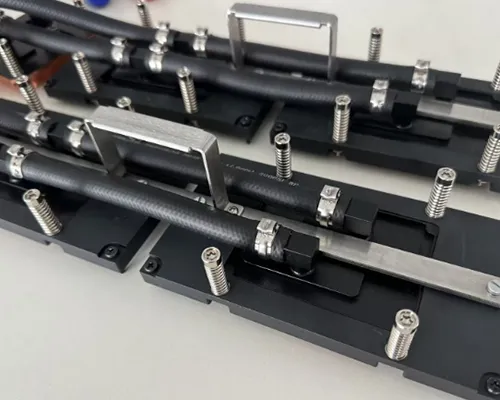