FSW Liquid cold plates
Friction Stir Welding is a process for producing liquid cooled plates that breaks through the limitations of traditional fusion welding, using mechanical force to dominate the thermoplastic process and reshape the bonding form of metal atoms in the solid state.
Get a Quotation
What is a FSW liquid cold plate?
Friction stir welding is a solid-state physical welding method. It usually consists of two parts: the bottom plate and the cover plate. Under the action of mechanical force and frictional heat, the stirring head moves relative to the welding material, causing the temperature of the friction surface and its surrounding area to rise to a temperature range close to but lower than the melting point of the welding material. The deformation resistance of the material decreases, the plasticity increases, and the interface oxide film is broken. Under the pressure of forging, the bottom plate and the cover plate are welded together through the diffusion and recrystallization of interface molecules. The entire process does not undergo chemical changes, making it a highly reliable liquid cooled plate production method.
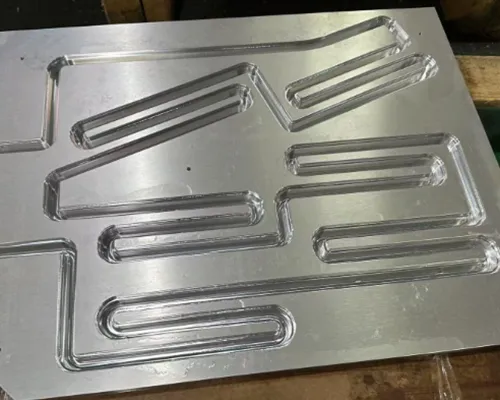
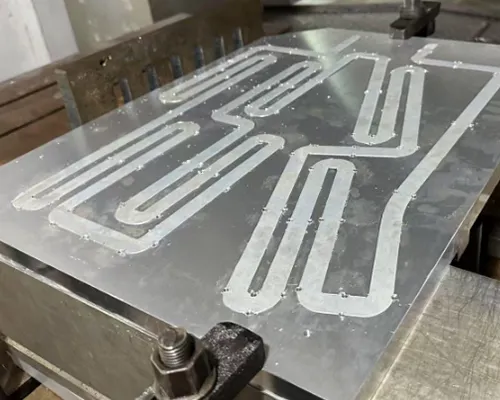
How to make a FSW liquid cold plate?
When manufacturing a friction stir welded liquid cooling plate, the selection of materials is crucial. Commonly used materials include aluminum and copper. In the case of aluminum materials, the bottom plate often adopts 6061 aluminum alloy, and the cover plate usually uses 1050 aluminum alloy. During production, the plates are first pre-treated, such as cutting and cleaning, to remove surface impurities and oil stains. Then, the bottom plate and the cover plate are assembled and positioned. Finally, a friction stir welding device is utilized, allowing the stirring head to rotate at a high speed and generate heat through friction with the materials. The materials are then fused in a plastic state to complete the welding and obtain the liquid cooling plate.
In the processing of the liquid cooling plate, the design and processing of the flow channel are of great importance. Generally, the width of the flow channel of the liquid cooling plate is between 9 and 20 millimeters, and the depth is approximately 10 millimeters. The thickness of the cover plate is usually 4 millimeters, while the bottom plate needs to have a concave-shaped groove. This structural design can ensure that after the cover plate is placed on it, it can create favorable conditions for the friction stir welding.To ensure the smooth progress of the processing, right angles should be avoided in the flow channel, and a transitional R-angle should be adopted to help the drill bit pass through smoothly. After the processing of the flow channel is completed, the material needs to be reshaped, and then CNC machining should be carried out to ensure that the thickness of the cover plate is not less than 3 millimeters. When welding, to ensure the welding quality, the welding depth generally needs to be greater than 4 millimeters.
How to design the flow channels for FSW liquid cold plate?
Local densification microchannels:
When designing a friction stir welded liquid cooling plate, for high power density heat sources such as inverters and IGBTs with a power exceeding 2000 watts, it is necessary to carry out local treatment on the flow channels of the liquid cooling plate. This is because the flow channels with a conventional unit area cannot meet the cooling requirements of high power density heat sources. Therefore, we usually carry out encryption treatment on the flow channels at the bottom of the heat source. That is to say, the flow channels at the bottom are fully in contact with the cooling liquid, so that the heat can be diffused into the cooling liquid and then carried away, thus ensuring that the high power density heat sources maintain an appropriate temperature during operation and guaranteeing the stable operation of the equipment.Usually, we use the skived fin process to produce these local densification microchannels.
Series connection:
When designing a liquid cooling plate, flow channel layout matters. For heat sources with power below 2 kW, a series – connection design is suitable.In this design, coolant enters the plate, flows through evenly – arranged channels, and exits. If there are multiple heat sources (e.g., 3 or 4) on the plate, the coolant passes through them one by one. As it absorbs heat, the first heat source is hotter than the last. But a temperature difference of about 4°C is acceptable.This simple series – connection approach is a common choice for medium – power heat sources, balancing cooling performance and design simplicity.
Parallel connection:
When designing liquid cooling plates for ultra-high power sources like inverters or IGBTs over 3000W, parallel flow channel designs are essential instead of series ones. Series designs cause large temperature differences among components, degrading performance.Parallel designs ensure uniform cooling but require precise control of flow rates beneath each heat source. Since lower pressure differences lead to faster flow, maintaining consistent flow rates across all parallel channels is crucial for efficient heat dissipation and stable equipment operation.
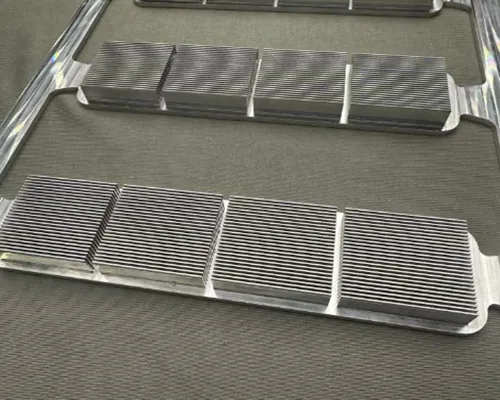
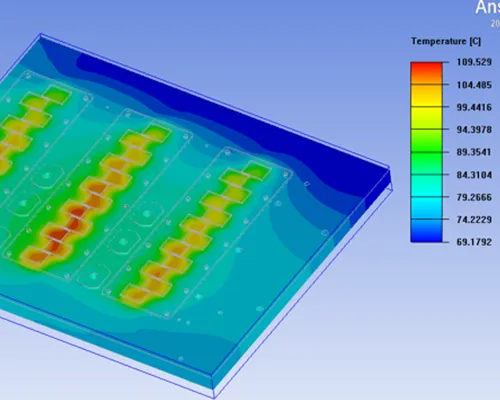
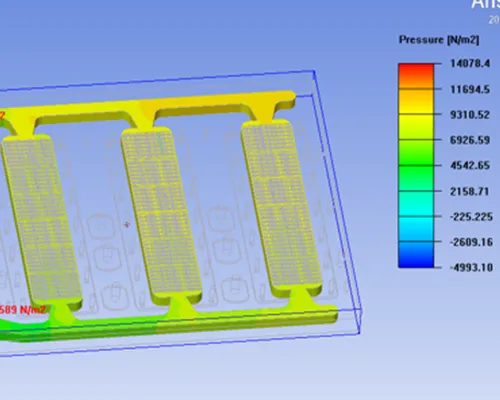
How does Walmate thermal make the FSW cold plate for customers?
Material
When it comes to material selection, we will determine whether to use the material of Copper 1100 or Aluminum 6063 according to the power level required by our customers. In this way, we can not only meet the customers' needs but also help them reduce costs.
Heat treatment
After selecting the material, we will conduct heat treatment on it. Since the raw material of the liquid cooling plate has internal stress, we need to anneal the material. This ensures that the internal stress can be released during the processing.
CNC machinning
We use our advanced CNC machines to precisely machine the flow channels , ensuring a high-precision tolerance match between the bottom plate and the cover plate. This precise machining process lays a solid foundation for the subsequent friction stir welding process.
Leakage test
Using air inspection or helium inspection methods to comprehensively check for any possible defects that may have occurred during the welding process. To ensure product quality, all liquid cooling plates are required to undergo a 100% leakage inspection. Only the liquid cooling plates that pass this inspection will proceed to the next step - precision CNC machining.
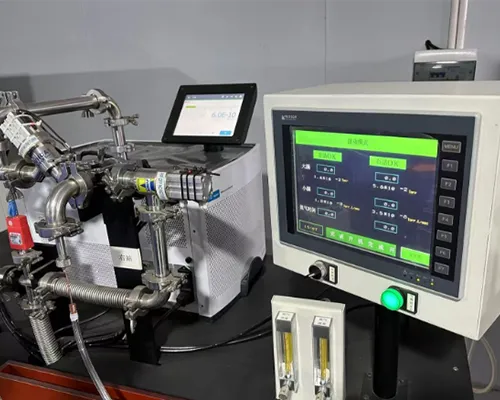
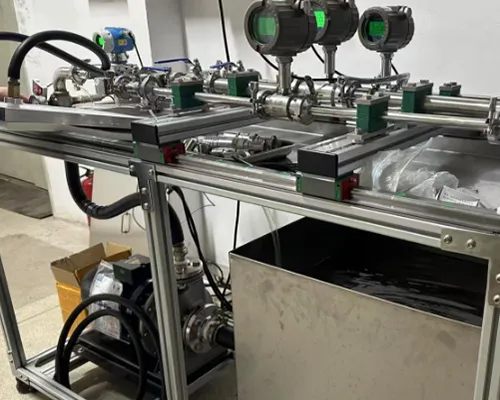