Epoxy-bonded fin heat sink
A heat sink made by bonding the bottom plate and fin of a heat sink together with epoxy resin as an adhesive, and utilizing the high bonding strength and good thermal conductivity of epoxy bonding.
What is an epoxy-bonded fin heat sink?
Epoxy bonded fin heat sink is a heat dissipation device that uses epoxy resin to firmly connect fins to the heat sink base. It effectively dissipates the heat generated by electronic devices and other devices by increasing the heat dissipation area and good thermal conductivity. It has the advantages of simple process, low cost, and high bonding strength, and is widely used in the field of electronics.
Its fins can be made of aluminum 1100 or 6063, or copper fins, and the base can be made of either copper or aluminum. This kind of combination of different materials can provide a very simple manufacturing process for the epoxy-bonded fin heat sink. All that’s needed is for the epoxy resin to have a sufficiently high thermal conductivity. This is a manufacturing process featuring flexible design for the epoxy-bonded fin heat sink.
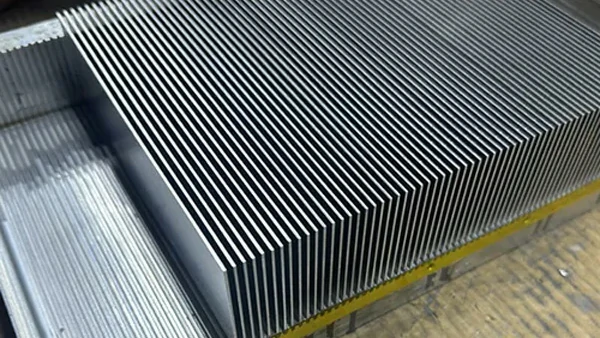
Characteristics of epoxy-bonded fin heat sinks
Convenient
Key feature of fin heat sinks bonded with epoxy-bended is that they do not require surface nickel plating treatment for heterogeneous materials such as copper and aluminum. Epoxy can directly bond these different metals without the need for additional nickel plating processes, simplifying manufacturing steps and reducing costs.
Unrestricted by technology
Unlike profile or die - cast heat sinks, epoxy - bonded fin heat sinks don't require high mold costs. They allow free combinations without constraints on fin thickness and spacing. Theoretically, there's no limit to height or space, maximizing the heat - dissipation area through this flexible approach.
High bonding strength
Epoxy resin can form a strong bond with various metal materials (such as aluminum, copper, etc.), making the fins tightly connected to the radiator base or other components, ensuring that they will not loosen due to factors such as vibration and thermal stress during long-term use, and ensuring the stability of the heat dissipation structure.
Process adaptability
It is usually composed of A and B resin components, mixed evenly and stirred in proportion. It can be cured at room temperature or lower temperature, with relatively low production process requirements, and can adapt to various manufacturing environments. Moreover, it can fill the small gaps between the fins and connecting components, compensate for dimensional errors, and improve the overall flatness and sealing of the structure.
How can we manufacture this epoxy-bonded fin heat sink for our customers?
Firstly and most importantly, we can use simple and cost-effective molds or adopt advanced laser cutting technology. These methods enable us to produce aluminum or copper fins with a thickness between 0.1 and 2.0 millimeters. The production cycle for molds and stamping dies is usually about two weeks, which ensures relatively fast delivery times for our clients’ projects.
Generally, epoxy resin glues made of two materials A and B are adopted. Through uniform stirring, the two materials can be evenly mixed together. However, it has a significant drawback, that is, its thermal conductivity is relatively low. Usually, the thermal conductivity coefficient (K value) is around 1.0 to 1.5w/(m.k). Therefore, we will recommend this process to customers with caution.
The heat sink connected with this kind of epoxy resin is actually an early production process. It emerged to make up for the limitations of profile heat sinks in producing fins with certain heights and spacings, and it also serves as a supplement to brazing or soldering processes. Relatively speaking, this process is inexpensive. However, with the advent of new processes like the skived fin heat sink process, this epoxy-bonded fin process is being used less and less.